How Plant Managers Can Prevent Unplanned Downtime
Reliability
How Plant Managers Can Prevent Unplanned Downtime
In a recent report published by ABB, alarming statistics have surfaced, revealing that unplanned downtime is exacting a heavy toll on producers, amounting to an astonishing $125,000 per hour. This eye-opening revelation underscores the critical importance of operator training in the realm of industrial operations, shedding light on its profound impact on mitigating avoidable downtime and its intricate relationship with ensuring plant reliability.
In this article, we'll explore the pivotal role operator training plays in reducing unnecessary downtime and how it intertwines with plant reliability.
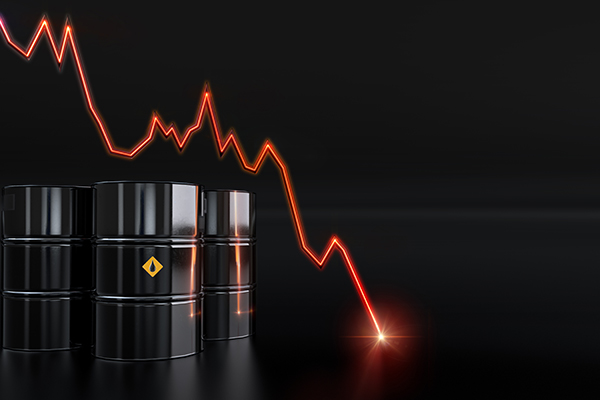
The Cost of Unplanned Downtime
Let's confront the undeniable fact - unplanned downtime is a financial nightmare for petrochemical businesses. According to the recent Sapio Research survey, a staggering 67% of companies face unplanned outages at least once a month. This means that these organizations are hemorrhaging hundreds of thousands of dollars each time their operations grind to an unexpected halt, which, for refineries and petrochemical plants, isn't just an inconvenience, it's a financial catastrophe.
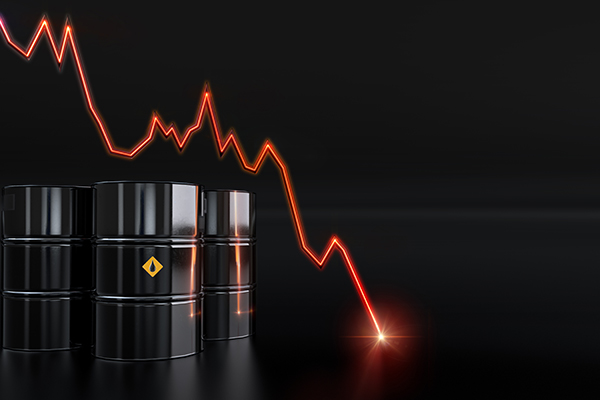
The ABB survey, aptly named the "Value of Reliability," highlights a crucial point - the correlation between reliability and unplanned downtime. In essence, the reliability of equipment and machinery is a linchpin in preventing unexpected shutdowns. But how does this connect with operator training?
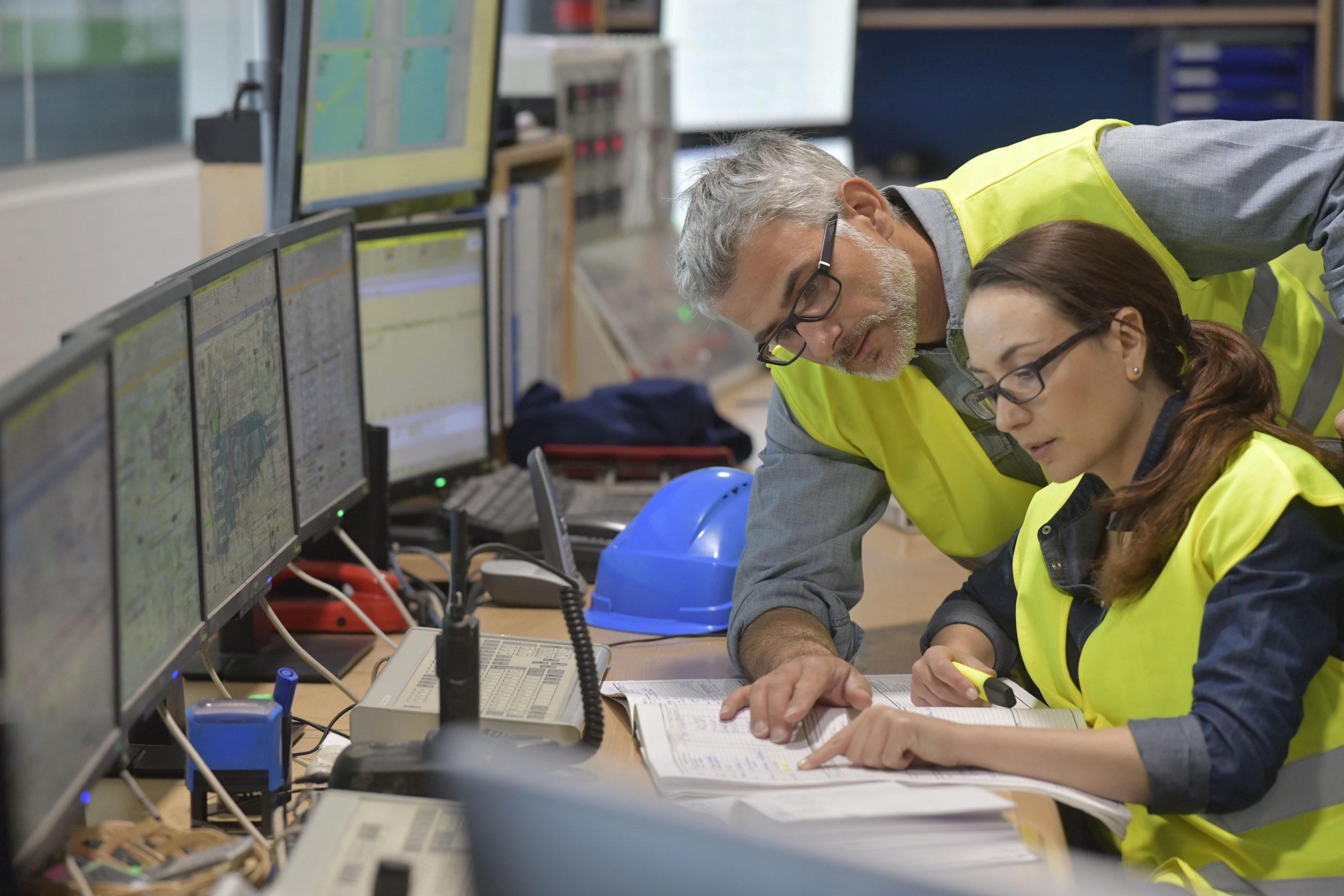
Operator Training: The Unsung Hero
Operator training is the unsung hero in the battle against unnecessary downtime. It's not just about teaching individuals how to push buttons and monitor gauges; it's about empowering them with the knowledge and skills to operate, maintain, and troubleshoot equipment effectively. However, here's the twist: while any operator training is indeed better than nothing, the real game-changer lies in engaging technical materials specifically designed to match how people learn. Here's why it's the ticket to saving money and enhancing reliability:
- Proactive Maintenance: When training is engaging, it enables operators to recognize early warning signs of equipment issues intuitively. This fosters proactive maintenance and repairs before minor glitches escalate into costly breakdowns.
- Efficient Troubleshooting: Well-designed training materials facilitate faster problem diagnosis. Operators grasp how to identify issues and take immediate corrective action, significantly reducing downtime.
- Optimal Operation: Interactive training helps operators fine-tune equipment settings and processes for peak efficiency, preventing premature wear and extending equipment lifespans.
- Enhanced Safety: Safety is paramount, and impactful training creates safe behaviors and habits, ensuring your operators make fewer errors that could lead to accidents or equipment damage.
- Data Empowerment: Operator training with a experiential approach includes data analysis and utilization instruction. This allows operators to make informed decisions based on performance data, further contributing to reliability.
The Interdependence of Training and Reliability
To underscore the interdependence of operator training and reliability, let's revisit the ABB survey. The fact that 21% of respondents still rely on run-to-fail strategies despite the exorbitant costs of unplanned downtime demonstrates a critical point. Operators are not fully aware of how reliable equipment directly impacts uptime, business reputation, and the bottom line. When operators receive comprehensive training, they not only understand the value of reliability but transform into champions of reliability within their organizations.
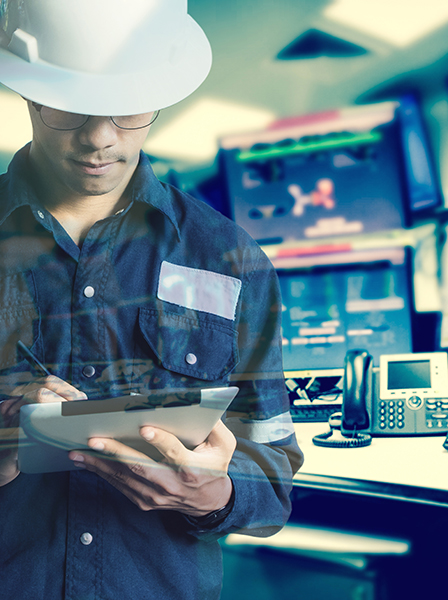
Unplanned downtime poses a formidable challenge to manufacturers, sapping productivity and profitability. The jaw-dropping $125,000 per hour figure serves as a stark reminder of the financial repercussions of overlooking this issue. While any operator training is a step in the right direction, engaging training materials take it to the next level. By investing in training materials that align with how people learn, manufacturers can empower their operators to operate, maintain, and troubleshoot equipment effectively, thus reducing downtime and safeguarding their bottom line. So, let's make engaging operator training the priority, ensuring that our facilities run smoothly, efficiently, and profitably. After all, a well-trained operator is the best defense against unplanned downtime.
Reference: Report: Unplanned Downtime Costs Manufacturers $125,000 per Hour